MANUFACTURER: INTERMAC
Design features:
Stand — The machine bed is made of particularly strong, electro-hardened steel and consists of a bottom frame that moves transversely along two rails and an upper frame that is attached to the bottom frame. The upper frame consists of lifting grippers with vacuum suction cups; both frames are driven by brushless motors.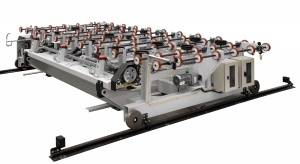
— The bottom table consists of motorized rollers. The barrels of the rollers rotate on calipers with bearings; the transmission is mechanical, chain-driven. The rollers have two operating speeds: fast for standard duty cycle and slow for sheet rollback from the cutting table. The movement is adjusted by means of an inverter.
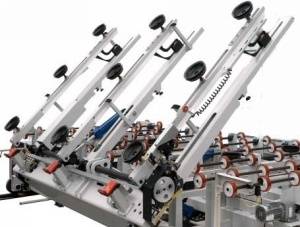
— The frames consist of 3 grippers, each with 3 vacuum suction pads. The grippers are connected by mechanical beams and rotary levers driven by oleodynamic cylinders. The grippers lift and feed the sheet onto the conveyor and then return to the original horizontal position.
Automatic alignment — The sheet is automatically aligned on the conveyor belt with the help of an ultrasonic sensor. At the same time as the rollers rotate, the table shifts transversely, aligning the glass.
The oleodynamic system is centralized, controlled by safety valves on each cylinder for frames and rollers. The central valve is mounted on the base of the machine.
Vacuum circuit — consists of a pump, vacuum switch and single-acting solenoid valve connected to suction cups. Each suction cup is equipped with a valve to disconnect from the main circuit.
Control panel — the control panel is installed in the operator’s work area. The panel is connected to the electrical cabinet mounted on the bed and controls all electrical parts. PLC and axis control is installed on the cutting table control computer.